Posts Tagged ‘Business & Industry Association of New Hampshire’
Tuesday, September 27th, 2011
The Community College System of New Hampshire (CCSNH) has been awarded $19.9 million, the largest grant in the System’s history, to develop training programs that will support NH’s advanced manufacturing industry.
The funds will enable the state’s seven community colleges, located in every region of New Hampshire, to develop programs that prepare individuals for skilled employment to meet current and emerging workforce needs in advanced manufacturing in New Hampshire. The programs will focus on displaced workers and other job-seekers by providing training opportunities at multiple professional levels in skills linked to regional employment.
The CCSNH grant proposal was titled the Regional Advanced Manufacturing Partnership: Elevating NH’s Workforce to Meet the High-Tech Skill Demands Of NH’s Rapidly Advancing Manufacturing Sector, or “Ramp-Up.” “This program is all about bringing high-quality jobs to New Hampshire, ensuring that we have the workforce to fill those jobs, enable business located here to grow, attract new companies, and increase economic activity,” said J. Bonnie Newman, Chancellor of the Community College System.
“Manufacturing is a critical driver of economic growth and employment in our state,” said U.S. Senator Jeanne Shaheen. “However, as businesses replace traditional manufacturing methods with advanced technology, many job-seekers have been unable to keep up because they lack the specialized skills required. By arming workers with the tools needed to excel in advanced manufacturing, this award will help New Hampshire workers secure high-paying jobs and help New Hampshire companies hire high-quality employees.”
“With manufacturing as such an important part of New Hampshire’s economy, a key part of our successful economic strategy has been training our workers in advanced skills so they can keep up with changing technology, and our businesses can continue to compete globally. This grant is exciting news for our state, our workers and our businesses. This is a tremendous amount of funding that will allow us to expand our worker training efforts, which will help more companies grow and compete,” Gov. Lynch said. “This is great news for New Hampshire’s economy.”
CCSNH’s efforts will target advanced manufacturing sub-sectors inculding automation and robotics, precision manufacturing, advanced machine tool technology, mechatronics, advanced materials technologies and composites, precision welding, automation and process control, and energy systems for precision manufacturing.
“This funding comes at a very important time, since students and the college population in New Hampshire have been disadvantaged by state budget cuts and decreased access to education and training opportunities,” said Newman. “While this grant will not replace state funds that were cut, it will make possible focused efforts in partnership with NH businesses to create educational and career ladders for advanced manufacturing jobs, a key industry here in New Hampshire and in the nation.”
“New Hampshire’s community colleges are uniquely situated to provide these opportunities and work in partnership with employers,” Newman said. “We have campuses in every region of the state. NH companies already look to the community colleges to train a local workforce in high-need skills like health care and technology. The community colleges are adept at providing access to students of all ages, backgrounds, and aspirations, and we have already developed strong partnerships that enable students to continue their education to the baccalaureate level and beyond.”
The CCSNH proposal was developed in close collaboration with over a dozen NH manufacturing companies from across the state. The industry partners provided data on current and future workforce needs, skills gaps of the current workforce and job applicant pool, industry trends, and specific equipment and types of training key to their ability to thrive and compete globally. Other partners in the application included the Business and Industry Association of New Hampshire, the NH High Tech Council, the Advanced Manufacturing Education Advisory Council, the NH Department of Resources and Economic Development, the NH Department of Labor, NH Employment Security, and the NH Department of Education.
Jim Roche, president of the Business and Industry Association of NH, said, “If we expect to retain and grow companies in New Hampshire’s leading economic sector – advanced manufacturing – we need to ensure alignment between training provided through our educational institutions and the needs of manufacturers and high technology employers. This grant represents a great opportunity to further that goal.”
George Bald, Commissioner of the NH Department of Resources and Economic Development, said, “This grant will have a tremendous impact on the NH workforce, on the quality of jobs that come to the state, and on the strength of the manufacturing industry in New Hampshire. The close collaboration between the community colleges and our NH employers to identify skill areas and training needs reflects the excellent working relationship that exists in New Hampshire to strengthen our workforce.”
CCSNH applied for the grant through the U.S. Department of Labor’s Trade Adjustment Act-Community College Career and Training Grant program.
Tags: Advanced Manufacturing Education Advisory Council, Business & Industry Association of New Hampshire, CCSNH, Community College System of New Hampshire, J. Bonnie Newman, Jeanne Shaheen, Jim Roche, New Hampshire Department of Education, New Hampshire Department of Resources & Economic Development, New Hampshire High Tech Council, NH Department of Labor, NH Employment Security, U.S. Department of Labor Posted in NH Business Matters | Comments Off on Manufacturing Industry in NH to Get $19.9 Million Shot-in-the-Arm
Monday, April 11th, 2011
Gov. John Lynch today unveiled a new Web site designed to better connect New Hampshire manufacturers with New Hampshire suppliers and buyers. The Web site is an outgrowth of a suggestion Gov. Lynch received from businesses during his Job Cabinet Roundtables.
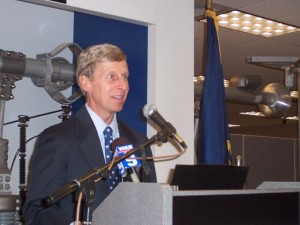 Governor John Lynch unveils the partnership between the State of New Hampshire and MFG.com.
The State is partnering with MFG.com, the largest global sourcing marketplace for the manufacturing industry, for this first-of-its- kind partnership. The unveiling took place at Burndy LLC, an electronic components manufacturer in Londonderry. Alan Beck, Burndy LLC Vice President of Application Tooling, made the suggestion for a better way for New Hampshire businesses to connect during the Manchester Jobs Cabinet Roundtable.
Gov. John Lynch joined representatives of several Granite State manufacturing firms and state economic development officials in unveiling the new site.
During Gov. Lynch’s Jobs Cabinet Roundtables last year, the Governor heard from business leaders who said it is a challenge for them to easily identify New Hampshire suppliers. A number of companies expressed a desire to contract with New Hampshire suppliers when at all possible rather than contracting out of state. The New Hampshire Division of Economic Development worked with MFG.com to develop this new Web site.
“We want to make it easier for New Hampshire businesses to support and work with other New Hampshire companies. That will help our businesses grow and create jobs here in the Granite State,” Gov. Lynch said. The more New Hampshire manufacturers can work with other New Hampshire companies, the stronger our economy will be.”
As part of the partnership, local companies registered on a special “New Hampshire only” page on MFG.com, will be able to purchase goods and services from each other, creating a heightened awareness of resources within the state.
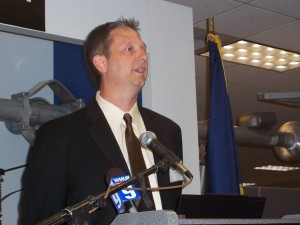 MFG.Com Senior Vice President Adam Oaks describes the many services that his company provides to the manufacturing community.
Adam Oaks, Senior Vice President and General Manager of MFG.com, stated that he believes this new partnership will open new doors for New Hampshire suppliers and buyers to engage in locally-based matchmaking.
“We are extremely excited to be part of this initiative that essentially enables the local New Hampshire manufacturing community,” he said. “The sourcing portal will effectively promote economic development within New Hampshire through intelligently connecting local manufacturing buyers and suppliers at the exact moment they need each other.”
The link for the specially designed page will be housed on NHEconomy.com, the State’s economic development Web site. Those suppliers who complete a registration for the MFG.com service through the New Hampshire landing page will receive an optimized profile, Atlas listing and projects from all Granite State buyers for $99 a month. Buyers registering via the landing page will have access to the New Hampshire information for free.
“What a wonderful way to stimulate commerce and build new relationships among New Hampshire manufacturers and prospective buyers,” said New Hampshire Department of Resources & Economic Development Director George Bald. “This first-in-the-nation pilot program gives our state an incredible edge as we further develop and strengthen our manufacturing sector.”
“A local supply base can provide a very competitive advantage particularly for developing new product and processes,” added Alan Beck, Burndy LLC Vice President of Application Tooling. Burndy has offered high quality, competitively priced connectors, wiring accessories and installation tooling that have solved connection problems for over 85 years. “The application that the Division of Economic Development and MFG.com have facilitated was created expressly for New Hampshire businesses and is a powerful tool that allows companies to easily find the core competencies that exist locally. This will create healthier businesses and a stronger local economy.”
“The New Hampshire page is of tremendous value to Granite State manufacturers,” Zenagui Brahim, director of operations for the New Hampshire Manufacturing Extension Partnership (MEP) said. “By giving us a new and innovative addition to our toolkit, we have improved the prospects for all engaged in this vital industry.”
A recent New Hampshire Center for Public Policy Studies report sponsored by the Business & Industry Association of New Hampshire and the New Hampshire High Tech Council noted that Smart Manufacturing/High Technology (SMHT) is the single largest sector of New Hampshire’s economy (19 percent). In 2009 alone, the SMHT sector encompassed 3,700 New Hampshire companies employing almost 80,000 people and paying out $6.4 billion in wages and benefits. Exports from the state’s manufacturers directly support more than 77,000 jobs, compared to about 52,000 jobs in travel and tourism.
The “New Hampshire only” MFG.com page can be accessed at www.mfg.com/nheconomy.
About MFG.com
MFG.com is the largest global sourcing marketplace for the manufacturing industry. MFG.com’s platform enables companies to intelligently connect, source, collaborate and perform due diligence with transparency and intellectual property protection. It supports virtually all manufacturing process and industrial components, is in seven major languages, more than 50 currencies and has more than 200,000 members on five continents. MFG.com is based in Atlanta and has offices in Shanghai and Paris. For more information: www.MFG.com.
Tags: Alan Beck, Burndy LLC, Business & Industry Association of New Hampshire, Job Cabinet Roundtable, MFG.com, New Hampshire Center for Public Policy Studies, New Hampshire Department of Resources & Economic Development, New Hampshire Division of Economic Development, New Hampshire High Tech Council, New Hampshire Manufacturing Extension Partnership, nheconomy.com, Zenagui Brahim Posted in NH Business Matters | Comments Off on Governor Announces First in Nation Partnership for State’s Manufacturers
Monday, February 7th, 2011
Here’s New Hampshire Business Resource Center Seacoast Business Services Specialist Christine Davis’ newest Portsmouth Herald column that answers the often tricky question: When does a hobby become a business?
I received several questions this past week on a variety of topics related to owning a business. It amazes me how much there is to know about business ownership and how little I actually know. I guess we all feel that way some days and can be thankful for having the Internet and colleagues to go to for help.
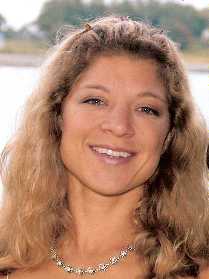 New Hampshire Business Resource Center Seacoast Business Services Specialist Christine Davis
Does a business need to make certain minimum revenue in order to be considered a business? I am just doing this on the side and don’t expect to earn much the first year in operation.
The simple answer is no. I went to www.irs.gov to get a more complete response for you and here is what they say: Generally, an activity qualifies as a business if it is carried on with the reasonable expectation of earning a profit. It gets a bit more complicated when you drill down to try and separate a hobby from a business as I learned from the site that you can actually deduct expenses from having a hobby. Really. I love this country.
NH is pretty easy as far as starting a business (assuming a permit isn’t required). You can register through the State by visiting www.sos.nh.gov/corporate and downloading the appropriate forms. The good thing about registering as a business, besides being a law-abiding citizen, is that you can deduct the expenses you incur that relate to your business.
I heard from another start-up this week:
Do I need to get a permit in order to start a photography business? Also, do I file for a business name the same time that I file as an LLC?
I smiled when I heard this question as I had just returned from the Business & Industry Association’s “Small Business Day at the State House” and had learned that NH requires permits from over 90 different business industries. I went to the following site, www.nh.gov/nhes/elmi/licertreg, to learn that while a Shampoo Assistant Apprentice does need to file for a license, a photographer does not.
As far as reserving a business name and filing to become an LLC, you need to first file for the name to ensure the name is available. This avoids needing to rewrite the articles of incorporation in the event that the name is not available. If the name is available, it can be held for 120 days to allow time to prepare the necessary documents needed for incorporation. More specific information can be found through the corporate division of the Secretary of State’s office website, www.sos.nh.gov.
I also wanted to thank those who wrote to me in response to the last article about health care costs and small businesses. I heard from a reader who suggested businesses also look into wellness programs to reduce costs. A healthier workforce will also be a more productive workforce. You should talk to your provider about these options. More information about the health care tax credit was requested and that can be found at the IRS website, www.irs.gov. Just type, health care tax credit for small employers, to be directed to the appropriate page.
Tags: Business & Industry Association of New Hampshire, Christine Davis, Internal Revenue Service, New Hampshire Business Resource Center, New Hampshire Secretary of State Posted in NH Business Matters | Comments Off on When Does a Hobby Become a Business?
Monday, January 24th, 2011
This column was authored by New Hampshire Business Resource Center Seacoast Business Services Specialist Christine Davis:
Before I started working for the Division of Economic Development, I had run two small non-profits here in New Hampshire. Due to their size and budget, health care coverage was not offered to the employees. The cost for a relatively young and healthy individual was a big and painful surprise to me. I could only imagine the financial pain inflicted on small businesses that are trying to offer health care to their employees.
I cringed when I heard from a business owner who wanted to know what he could do to lower his health care costs. He had just learned that his costs were going to rise by $1,000 per month this year. Every year his costs have increased and like most businesses, he has seen a dip in revenue over the past 18 months. The reason why I cringed is two-fold. First, the financial increase he stated is just crazy. Second, I don’t have any answers that can eliminate his problem and I hate that.
Although I don’t possess a magic wand (something my seven-year-old thinks she can get from the tooth fairy), I do have some thoughts I can share which might be helpful. It is important that as a business owner you go over your policy with your provider to make sure everything is accurate and up to date. Are there any new plans that might fit your company and reduce costs? Have you talked to any other providers? There aren’t a lot of options but you need to look at them all before you settle for one. You can go to www.nh.gov/insurance to learn more about providers in the State and up to date insurance information.
One option that has been gaining more subscribers is the high deductible plan. I switched to one myself a year ago to reduce my premiums. It may lower your premium but you need to be prepared to cover a higher deductible, which can amount to some hefty out of pocket expenses if you have an unexpected injury or illness. If you decided to go the high deductible route, you can buffer it with a Health Savings Account (HSA).
An HSA is an account that you can put money into to save for future medical expenses. There are certain advantages to putting money into these accounts including favorable tax treatment.
I also want to remind small business owners of the tax credit that became available as of December 2010. If your business has less than 25 full-time employees or 50 half-time employees and the average pay is less than $50,000.00, you very well may be eligible for up to a 35% tax credit. That credit will increase to 50% in 2014. There is a gradual phase out with wages between 25-50k and 10-25 full-time workers. Non-profits can receive up to a 25% tax credit that will increase to 35% in 2014. This tax credit can have some real positive impact on small businesses that are covering at least half of the cost of their employees’ health care.
There are so many reasons why our health care costs have gotten out of control. While I can’t reform the system or get Americans to take better care of their health, I can recommend that you look into the above listed options and talk to your local legislators to learn where they’re at on the issue. Those individuals can be found by visiting www.gencourt.state.nh.us. If you are looking for change, reach out to those who have the power to make those changes. On February 1st, you can attend the Small Business Day at the Holiday Inn in Concord to hear from health care experts on the high cost of health insurance and what suggestions they have for reducing those costs. You can register for this morning event, a joint effort supported by the Division of Economic Development, the Business and Industry Association of NH and numerous business support organizations, by visiting www.nhbia.org.
Tags: Business & Industry Association of New Hampshire, Christine Davis, New Hampshire Business Resource Center, New Hampshire Division of Economic Development Posted in NH Business Matters | Comments Off on A Prescription for Small Business Owners
Wednesday, January 12th, 2011
A discussion about strategies and opportunities for controlling healthcare costs, a look at this year’s top policy issues from the state’s top legislators and more will be the focus of the Business and Industry Association’s 6th Annual Small Business Day at the State House event to be held Feb. 1 at the Holiday Inn, Concord from 7:30 to 11:30 a.m.
The annual small business event, held in partnership with the New Hampshire Small Business Development Center (NH SBDC), New Hampshire Division of Economic Development, and local and regional chambers of commerce and business associations, is meant to engage small business owners and managers in public policy discussion and debate, as well as provide them with practical and relevant information to help manage and grow their business. Small Business Day is sponsored by Public Service of New Hampshire, Anthem Blue Cross and Blue Shield of New Hampshire, and media sponsor New Hampshire Business Review.
Small Business Day at the State House will begin with a panel discussion with the state’s top elected leaders: Senate President Peter Bragdon, House Speaker Bill O’Brien, Senate Democratic Leader Sylvia Larsen and House Minority Leader Terie Norelli (awaiting confirmation). The state leadership panel will focus specifically on top small business issues of 2011 and how state elected leaders will resolve them.
Following a short break, a panel of experts in the healthcare sector will participate in a panel discussion titled “Health Care – Why Is It So Expensive and What Can My Small Business Do About It?” Panel participants include Lisa Guertin, president of Anthem Blue Cross and Blue Shield in New Hampshire; Steve Gerlach, an attorney with Bernstein Shur; and Dan Cronin, CEO of CGI Employee Benefits Group. They will explore various theories about why health care is so expensive in the Granite State and discuss strategies and opportunities for small businesses to control rising healthcare costs.
The New Hampshire Small Business Development Center will present the event’s final breakout session titled “Move Your Business Forward with e-Tools,” a preview of two of the center’s new e-courses. Hollis McGuire of the NH SBDC will discuss the course Financing a Business in NH, which covers the variety of financing options available to New Hampshire small business owners. Christine Halvorson of Halvorson New Media will outline the second course, Social Media for Business, which unravels the array of products and uses of social media for business.
Participating chambers and business associations include the Grantham Area, Greater Claremont, Greater Keene, Greater Peterborough, Greater Salem, Hampton Area, Hillsborough, Lakes Region, Lebanon Area, Lincoln-Woodstock, Merrimack, Plymouth Regional, Souhegan Valley, Waterville Valley Region and Wolfeboro Area chambers of commerce, the New Hampshire Association of Insurance Agents, and the New Hampshire High Technology Council.
The cost to attend Small Business Day at the State House is $15 per person and includes continental breakfast. To register, call 603-224-5388 x116 or visit nhbia.org.
Tags: Anthem Blue Cross and Blue Shield of New Hampshire, Bernstein Shur, Business & Industry Association of New Hampshire, CGI Employee Benefits Group, Christine Halvorson, Dan Cronin, Halvorson New Media, Hollis McGuire, Lisa Guertin, New Hampshire Business Review, New Hampshire Division of Economic Development, New Hampshire Small Business Development Center, Peter Bragdon, Public Service of New Hampshire, Steve Gerlach, Sylvia Larsen, Teri Norelli Posted in NH Business Matters | Comments Off on Strategies for Managing Healthcare Costs Focus of Panel at Small Business Event
Thursday, October 21st, 2010
It was a real pleasure for the New Hampshire Division of Economic Development to be a sponsor of last night’s New Hampshire Business Review “Business Excellence Awards” at Southern New Hampshire University. This was a great celebration of New Hampshire’s best and brightest companies and the good folks at NHBR were rewarded for their hard work with a packed room.
Special congrats are in order for “No Bull Business Blog” guest blogger Dr. Russ Ouellette of Sojourn Partners who was recognized with an award in the “Business Services” category. Way to go Russ!!
Here’s a recap of last night’s festivities:
New Hampshire Business Review honored 14 individuals at the 2010 Business Excellence Awards, which recognize the efforts and achievements owners of businesses with 100 employees or fewer.
More than 50 nominations in 13 categories were received, making the job of the 14 judges that much more difficult.
More than 300 people attended the Oct. 20 event, which was held at Southern New Hampshire University in Manchester.
Because of the extraordinary number of accomplished candidates, NHBR also named a tie in the Retail category and finalists in several other categories.
NHBR also announced two inductees into the Business Excellence Hall of Fame, which singles out people whose entire careers have been marked by a consistent and impressive record of accomplishments, both in their chosen fields, in their communities, and across the state and beyond. These honorees were selected by a separate panel of judges.
“Each of the businesspeople who receive these honors has a different story to tell,” said Sharron McCarthy, president of McLean Communications and publisher of NHBR. “But what they have in common is determination, industriousness and the ability to come up with innovative solutions that have allowed their businesses to survive and thrive, regardless of economic conditions, and a commitment to serving their communities.”
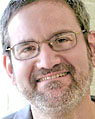 NHBR Editor Jeff Feingold
Jeff Feingold, editor of NHBR, said, “We would like to salute all of the nominees, the people who nominated them and the winners themselves for their contributions toward making New Hampshire a great place to do business.”
Emcee was Charlie Sherman, host of WGIR-AM’s morning news talk program.
A portion of the proceeds from the evening benefited Court Appointed Special Advocates, or CASA, which advocates for New Hampshire children in the state’s court system in cases of neglect and abuse.
The winners of the 2010 NHBR Business Excellences Awards were:
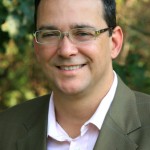 "Business Services" winner Dr. Russ Ouellette
• Excellence in Business Services — Russ Ouellette, Sojourn Partners LLC, Bedford
• Excellence in Construction — G. Hayden McLaughlin, Belknap Landscape Co., Inc., Gilford
• Excellence in Financial Services — Frank Teas, The Nashua Bank
• Excellence in Health Care — Joshua Siegal, M.D., Access Sports Medicine & Orthopaedics, Exeter
• Excellence in Hospitality — Carol Sheehan, The Red Arrow 24 Hr. Franchising Inc., Manchester
• Excellence in Media & Marketing — Linda Fanaras, Millennium Integrated Marketing Inc., Manchester
• Excellence in Nonprofits — Peter Kelleher, Partnership for Successful Living, Nashua
• Excellence in Professional Services — Jonathan Halle, Warrenstreet Architects, Concord
• Excellence in Real Estate — Quentin Keefe, Regency Mortgage Corp., Manchester
• Excellence in Retail (tie) — Susan Lozier Robert, Frederick’s Pastries, Amherst; Curt Jacques, West Lebanon Feed & Supply
• Excellence in Technology — Jason Alexander, Alexander Technology Group, Bedford
The 2010 NHBR Business Excellence Hall of Fame Inductees were:
• Alex Ray, founder, Common Man Family of Restaurants
• Lew Feldstein, former chairman, New Hampshire Charitable Foundation
The judges for the 2010 NHBR Business Excellence Awards were:
• Jennifer Boulanger, loan officer at Capital Region Economic Development Corp. in Concord and former executive director of the Belknap County Economic Development Council based in Laconia
• Robin Comstock, president and CEO, Greater Manchester Chamber of Commerce
• Roy Duddy, interim director, New Hampshire Division of Economic Development
• Lou Guevin, former chairman, Junior Achievement of New Hampshire
• Julie Gustafson, president and CEO, Amoskeag Business Incubator, Manchester
• Richard Hanson, professor, accounting and taxation, Southern New Hampshire University, Manchester; executive director, Institute for Forensic Accounting and Fraud Examination, SNHU
• Mahboubul Hassan, professor, economics and finance, SNHU
• Lise Howson, vice president and business banking relationship manager, Citizens Bank
• Witmer Jones, New Hampshire district director, U.S. Small Business Administration
• Dave Juvet, senior vice president, Business & Industry Association of New Hampshire
• Patrick F. McDermott, economic and community development manager, Public Service Company of New Hampshire
• Tim Sink, president, Greater Concord Chamber of Commerce
• Ashley Smith, business editor, The Nashua Telegraph
• Chip Underhill, senior marketing manager, FairPoint Communications, Manchester
Sponsors of the event were FairPoint Communications, Laconia Savings Bank, Harvard Pilgrim Health Care of New England, Public Service of New Hampshire, J Maze Design, New Hampshire Division of Economic Development, Merrimack Street Volvo, WGIR-AM 610, New Hampshire Public Television and Southern New Hampshire University. — NEW HAMPSHIRE BUSINESS REVIEW
Tags: Alex Ray, Alexander Technology Group, Ashley Smith, Belknap Landscape Co., Business & Industry Association of New Hampshire, Capital Region Economic Development Corp., Carol Sheehan, CASA, Charlie Sherman, Chip Underhill, Citizens Bank, Common Man Family of Restaurants, Curt Jacques, Dave Juvet, FairPoint Communications, Frank Teas, Frederick's Pastries, G. Hayden McLaughlin, Greater Concord Chamber of Commerce, Greater Manchester Chamber of Commerce, Harvard Pilgrim Health Care of New England, J Maze Design, Jason Alexander, Jeff Feingold, Jennifer Boulanger, Jonathan Halle, Joshua Siegal M.D., Julie Gustafson, Junior Achievement of New Hampshire, Lew Feldstein, Linda Fanaras, Lise Howson, Lou Guevin, Mahboubul Hassan, Merrimack Street Volvo, Millenium Advertising, Nashua Telegraph, New Hampshire Business Review, New Hampshire Charitable Foundation, New Hampshire Division of Economic Development, New Hampshire Public Television, Partnership for Successful Living, Pat McDermott, Peter Kelleher, Public Service of New Hampshire, Quentin Keefe, Regency Mortgage Corp., Richard Hanson, Robin Comstock, Roy Duddy, Russ Ouellette, Sharron McCarthy, Sojourn Partners, Southern New Hampshire University, Susan Lozier Robert, The Nashua Bank, The Red Arrow, Tim Sink, U.S. Small Business Administration, Warrenstreet Architects, West Lebanon Feed & Supply, WGIR-AM, Witmer Jones Posted in NH Business Matters | Comments Off on Winners Celebrated at 8th Business Excellence Awards
Friday, August 20th, 2010
Charles E. “Gus” Whalen Jr. has boldly gone where other business owners can only dare to dream. In addition to operating the Warren Featherbone Company, a major children’s wear manufacturing facility in Gainesville, GA, Whalen has overseen the development of the Featherbone Communiversity, a collaborative, cross-generational learning alliance that allows entrepreneurial ideas to take flight. Clearly, this isn’t your “grandfather’s CEO.”
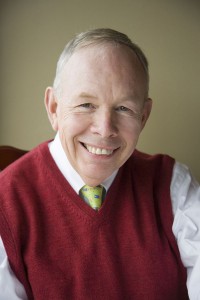 Gus Whalen
Whalen, keynote speaker at the Eighth Annual Governor’s Advanced Manufacturing & High Technology Summit scheduled for September 28th from 7 a.m.-2 p.m. at the Radisson Hotel in Manchester, also directs the efforts of The Warren Featherbone Foundation and is author of “The Featherbone Principle,” “The Featherbone Spirit,” “The Gift of Renewal” and “Hooked at the Roots – the Evolution of Featherbone Communiversity.”
“Warren’s work has not only transformed the manufacturing industry, but also the way that communities are built and sustained,” said New Hampshire Manufacturing Extension Partnership Director of Operations Zenagui Brahim. “By constantly reinventing his company and taking the additional step of creating innovative learning centers like the Communiversity, he has proven to be one of our nation’s true visionaries.”
Developed by the Business & Industry Association of New Hampshire, the New Hampshire Manufacturing Extension Partnership, the New Hampshire Division of Economic Development and the New Hampshire High Technology Council, the summit will bring together industry leaders for a day of information sharing, networking and best practices.
In addition to the keynote address by Gus Whalen as well as a related interactive session, the summit will feature a series of workshops including “Is Everyone In Your Organization Working Effectively Toward the Same Ends?,” “How Are You Sustaining Lean?” and “Advancing Talent Management.” New Hampshire Department of Resources & Economic Development Commissioner George Bald will also give an overview of the state’s manufacturing industry.
The 8th Annual Governor’s Advanced Manufacturing & High Technology Summit is sponsored by Citizens Bank, BAE Systems, APICS, the Society of Manufacturing Engineers and media sponsor New Hampshire Business Review. The registration fee is $95 per person and includes lunch. For more details, visit www.nhbia.org.
Tags: Business & Industry Association of New Hampshire, Communiversity, Gus Whalen, New Hampshire Department of Resources & Economic Development, New Hampshire Division of Economic Development, New Hampshire High Technology Council, New Hampshire Manufacturing Extension Partnership, Radisson Hotel, Warren Featherbone Company, Zenagui Brahim Posted in NH Business Matters | Comments Off on Collaboration Focus of Manufacturing Summit
Tuesday, September 29th, 2009
The New Hampshire Manufacturing Extension Partnership (NH MEP) today announced the results of the first national survey of world-class manufacturers, hailing the findings as valuable to both state policymakers and New Hampshire companies.
Based on an in-depth national survey of more than 2,500 manufacturers, including 74 firms in New Hampshire, the study identifies six crucial strategies necessary for world-class manufacturing success. The most unique aspect of the ground-breaking study, however, is the evaluation instrument utilized in the study. It provided participating manufacturers with a detailed assessment of how their management practices compare to global industry leaders and can evaluate whether individual firms are implementing the procedures and strategies that will enable them to thrive and succeed in the coming decade.
“The Next Generation Manufacturing Study is probably the most exhaustive and detailed survey of the US manufacturing base ever conducted. In today’s climate of globalization and the threat of lost manufacturing jobs, it’s important to know where the U.S. stands as a player in the international market. The study was also illustrative for Graphicast, as it highlighted where we stand compared to the more than 1,000 companies that responded to the study. This information gives us a clear path to follow to achieve world class status in technology and service,” said Val Zanchuk, president of Jaffrey-based Graphicast.
New Hampshire manufacturers like Graphicast that participated in the study received a free customized benchmarking report comparing their progress to the overall state and national results. Each confidential benchmarking report was prepared by the respected research and strategic consulting firm, the MPI Group.
Commissioned by Manufacturing Extension Partnership (MEP) centers across the country, including NH MEP, and the American Small Manufacturing Coalition, the study offers the most detailed description yet of what it takes for American manufacturers to compete in the global economy. The study was designed as the first step in a long-term effort to help U.S. manufacturers survive the recession and renew America’s manufacturing leadership over the next decade.
“New Hampshire’s economic recovery depends on the ability of its manufacturers to maintain profitability in the face of fierce competition. Manufacturing remains the state’s largest industry in terms of gross state product, accounting for more than 13 percent of state GDP. The challenge to policymakers is not to give up on manufacturing but to support the transformation of the state’s manufacturing sector into a faster, more flexible industry capable of outperforming their non-world-class peers,” said Zenagui Brahim, NH MEP director of operations.
“The study itself is only the first step in NH MEP’s efforts to assist local manufacturers,” Brahim stated. “Although the national study is complete, New Hampshire manufacturers can take advantage of the evaluation instrument and work with NH MEP project managers to conduct an assessment of their company’s strategic policies, investments and performance. Every manufacturer in the state has the ability to utilize this valuable new resource.”
The Keys to Next Generation Manufacturing Success
Next Generation Manufacturing (NGM) refers to a framework of strategies that will drive manufacturing growth in the 21st century. Developed by leading manufacturers, industry thought leaders and the MEP centers, Next Generation Manufacturing reflects the best practices and performance strategies of world class companies. To remain competitive, manufacturers in New Hampshire and across the country need to achieve world-class performance in at least some of these key areas. The study identifies six essential strategies:
• Customer-focused innovation: Deliver new and better customer solutions at a faster pace than the competition.
• Advanced talent management: Secure a competitive performance advantage by having superior systems in place to recruit, hire, develop and retain talent.
• Systemic continuous improvement: Record annual productivity and quality gains that exceed the competition through a companywide commitment to continuous improvement.
• Extended enterprise management: Leverage a flexible network of supply chains and partnerships to provide competitive advantages of speed, cost and quality.
• Sustainable product and process development: Design and implement waste and energy-use reductions at a level that provides superior cost performance and recognizable customer value.
• Global engagement: Secure business advantages through people, partnerships and systems capable of engaging global markets, talent and resources.
The survey administered to the initial 1,500 companies nationwide employed 63 questions to drill down and measure each firm’s progress, or lack of progress, in implementing strategies in these six essential areas.
Sobering Findings
• A serious gap exists between the strategies that New Hampshire and U.S. manufacturers believe are critical to their future success and their actual progress in implementing those strategies. Currently, only a fraction of New Hampshire manufacturers are at or near world-class in any of the six NGM strategies.
• Small and midsize manufacturers are less likely than larger firms to be at or near world-class status in each of the NGM strategies. One-third of respondents nationwide with less than $10 million in revenue were not at or near world-class in any strategy, compared to just 14% of manufacturers with more than $100 million in revenue.
• Measurement systems are inadequately deployed. Even in one of the most fundamental and easiest-to-measure areas – process improvement – 46% of respondents in New Hampshire and across the country had no measurement system or only ad hoc measurement systems.
• Effective partnerships with employees, suppliers and regional support organizations are the exception rather than the norm. Nationwide, a majority of respondents (56%) engage less than half of their employees in improvement initiatives, falling far short of industry best practices that require company-wide participation. In New Hampshire the results were modestly better, but 45% of respondents still engage less than half of their employees.
• In New Hampshire and across the nation approximately 40% of companies fail to reach or approach world-class status in the ability of their supply chains to respond to unexpected customer demand for existing products. In part this is due to the failure of companies to implement supply-chain measurement systems. More than 45% of New Hampshire firms said that they have no measurement system or only ad hoc measurement systems in place to review the return from supply chain management and collaboration.
• Energy efficiency remains a weak link. Less than five percent of New England firms are at or near world-class status in terms of annual reduction of energy consumption per unit of product output.
• Only 28% of respondents nationwide and 35% of firms in New Hampshire believe global engagement is highly important, despite a near-term future in which markets, talent, competitors and partner opportunities are growing faster outside the U.S. than within its borders.
New England’s Strength: Advanced Manufacturing
The survey data reveal a sobering picture of the challenges facing American manufacturers. But the report highlights an important distinction that characterizes New England manufacturers in general and New Hampshire manufacturing sector in particular. New England possesses a robust advanced manufacturing cluster that distinguishes itself from manufacturers nationwide in some very notable ways.
• New England manufacturers devote more resources to new product development and R&D than their counterparts nationwide.
o 23.8% of New England manufacturers invest more than ten percent of sales in new product development versus 14.6% of firms nationwide.
o 48.9% of New England manufacturers dedicate more than five percent of their workforce to new product development versus 34.6% of firms nationwide.
• New England manufacturers launch significantly more new products annually than their counterparts nationally (23.5% of New England manufacturers launch more than ten percent of their total SKUs annually versus 15.7% nationally.)
• New England manufacturers derive a significantly larger percentage of annual sales from new products than their counterparts nationally (33.7% of New England manufacturers derive at least one-quarter of their annual sales from products introduced in the last three years versus 24.8% of manufacturers nationally.)
• New England manufacturers derive significantly more value-added per employee than their counterparts nationwide, with 34.9% of New England respondents reporting that they receive more than $125,000 per employee versus 28.0% nationwide achieving that level of value-added.
These findings confirm the results of another recent study on manufacturing conducted by Deloitte Consulting LLP for the New England Council, which found that New England enjoys a strong cluster of advanced manufacturers whose productivity improvements have been transformational. That report, Reexamining Advanced Manufacturing in a Networked World: Prospects for a Resurgence in New England, noted that advanced manufacturing has reversed the decline associated with traditional manufacturing in New England by developing a talent-rich network of advanced manufacturers with skilled workforces capable of creating complex product solutions.
“New England manufacturers clearly out-perform their counterparts nationally in terms of developing new products and gaining a higher value-add from each employee. But the Next Generation Manufacturing study clearly shows how far many manufacturers still have to go to reach world-class status,” said NH MEP Operations Director Brahim. “In many strategic areas our state’s firms are just as challenged as manufacturers nationwide and need to take major steps to improve their performance or else risk being left behind by the global competition. New England’s economic future will be determined by how the region’s manufacturers respond to this challenge.”
Attention manufacturers! Growth and sustainability will be the theme of the seventh annual Governor’s Advanced Manufacturing and High Technology Summit, scheduled to take place from 7 a.m. to 2 p.m. on Tuesday, Oct. 13, at the Grappone Conference Center in Concord.
Coordinated by the New Hampshire Division of Economic Development, the New Hampshire Manufacturing Extension Partnership and the Business & Industry Association of New Hampshire, the summit will provide participants with tips for accelerating reliable growth in their businesses.
Sponsors of the event are Citizens Bank, the Society of Manufacturing Engineers, the Association for Operations Management and New Hampshire Business Review.
Registration fee for the summit is $85 per participant; lunch is included. Interested parties can sign up online by visiting http://www.acteva.com/ttghits.cfm?EVA_ID=23444.
Tags: American Small Manufacturing Coalition, Association for Operations Management, Business & Industry Association of New Hampshire, Citizens Bank, Governor's Advanced Manufacturing and High Technology Summit, Graphicast, Grappone Conference Center, MPI Group, New Hampshire Business Review, New Hampshire Division of Economic Development, New Hampshire Manufacturing Extension Partnership, Next Generation Manufacturing Study, Society of Manufacturing Engineers, Val Zanchuk, Zenagui Brahim Posted in NH Business Matters | Comments Off on National Manufacturing Survey Results Announced
Wednesday, September 2nd, 2009
Growth and sustainability is the theme of the 7th Annual Governor’s Advanced Manufacturing and High Technology Summit scheduled to take place on Tuesday, October 13th from 7 a.m.-2 p.m. at the Grappone Conference Center.
Coordinated by the New Hampshire Division of Economic Development, the New Hampshire Manufacturing Extension Partnership (NH MEP) and the Business & Industry Association of New Hampshire and sponsored by Citizens Bank, the Society of Manufacturing Engineers, the Association for Operations Management and New Hampshire Business Review, the summit will provide participants with tips for accelerating reliable growth in their businesses.
Morning speaker Beth Goldstein, author of The Ultimate Small Business Marketing Toolkit, will lead participants in an interactive discussion on the art of developing a powerful brand based on customers’ needs, spending patterns, pain points and the value they derive from your company.
Later workshops will center around the following subjects: “Case Studies on Lean Green and Energy” (Jay Fallon, Continuous Improvement Manager, BAE Systems and Art Christianson, Vice President of Manufacturing, High Liner Foods), “Growing Your International Business: Successful Export Growth Strategies” (Michael Stone, Stone & Associates, Dawn Wivell, Director, NH International Trade Resource Center and Justin Oslowski, Director, NH Export Assistance Center, U.S. Department of Commerce), and “Introducing a System for Reliable Growth” (Patricia Giavara, Assistant Director and Growth Coach with the Vermont Manufacturing Extension Center and Jane Ely, NH MEP Project Manager).
Keynote speaker Michael Reopel, Principal of Deloitte Consulting, will present the results of his report “Reexamining Advanced Manufacturing in a Networked World – Prospects for Resurgence in New England.” This report identified five subsectors within the New England manufacturing industry that are poised for growth, discussed the challenges that these industry subsectors face and identified the opportunities they provide for sustainable economic growth even during these difficult economic times.
The registration fee for the summit is $85 per participant; lunch is included. Interested parties can sign up online by visiting www.nhbia.org’s “Calendar” page and clicking on October 13th. For more information, call Zenagui Brahim or Cathy Doty at the NH MEP at (603) 226-3200.
Tags: Art Christianson, Association for Operations Management, BAE Systems, Beth Goldstein, Business & Industry Association of New Hampshire, Cathy Doty, Citizens Bank, Dawn Wivell, Deloitte Consulting, Grappone Conference Center, High Liner Foods, Jane Ely, Jay Fallon, Justin Oslowski, Michael Reopel, Michael Stone, New Hampshire Business Review, New Hampshire Division of Economic Development, New Hampshire Manufacturing Extension Partnership, NH Export Assistance Center, NH International Trade Resource Center, Patricia Giavara, Society of Manufacturing Engineers, Stone & Associates, The Ultimate Small Business Marketing Toolkit, U.S. Department of Commerce, Vermont Manufacturing Extension Center, Zenagui Brahim Posted in NH Business Matters | Comments Off on 7th Annual Governor’s Advanced Manufacturing & High Tech Summit Scheduled
|